纺织机械细长轴加工工艺研究
1 细长轴加工工艺特点
细长轴类零件的加工是一项工艺性较强的综合技术[2]。由于细长轴本身刚性差(L/d值愈大,刚性愈差),在车削和磨削过程中会出现较多的问题。
(1)刚性差。工件受切削、磨削力,自重和旋转时离心力的作用,会产生弯曲、振动,严重影响其圆柱度和表面粗糙度。
(2)热变形大。在切削过程中,工件受热伸长使刚度进一步降低,加剧工件产生弯曲变形,工件受热产生弯曲变形,车削和磨削就很难进行,严重时会使工件在顶尖间卡住。
(3)废品率高。采用跟刀架,中心架等辅助工夹具使操作技能要求提高,从而使机床、工夹刀具等多方面的协调困难,增加了许多震动因素,这都对加工精度产生诸多不良影响,使工件容易出现翘曲、振纹、锥度大、竹节等疵病而报废[2]。
车削和磨削细长轴的难度较大,但它也有一定的规律性,主要抓住中心架和跟刀架的使用、解决工件热变形伸长以及合理选择车刀几何形状等三个关键技术,控制好切削深度、走刀量、机床转速三要素,问题就迎刃而解了。
2 材料准备
本文采用纺织机械传动主轴,材料为40Cr,外形尺寸为φ45mm×1265mm,加工后成品外形尺寸要求为φ40mm×1260mm,如图1所示,其化学成分如表1所示。
由于传动主轴要求有较高的强度,韧性及良好的综合机械性能,要求在车削之前对其进行调质热处理,且调质处理能使工件的刚性大大加强,有利于切削加工。加工中传动主轴的热处理工艺确定为:850℃油淬+520℃高温回火。由于调质处理影响传动主轴的直线度,故在车削加工前对调质后圆跳动较大的传动主轴进行校直处理。
成品传动主轴的主要技术要求如下:
1.外径尺寸:φ40H8;
2.表面粗糙度:Ra≤1.6。
3.全长径跳:径跳<0.02mm;
3 细长轴车削加工工艺研究
3.1合理选择定位基准
切削中定位基准的选择是十分重要的,定位基准选择不当会产生较大的定位误差,进而产生较大的加工误差。所以装夹工件时要合理选择定位基准,轴类零件的定位基准,最常用的为两顶尖孔。因为细长轴类零件外圆表面、锥孔、螺纹表面的同轴度,以及端面对轴线的垂直度是其相互位置精度的主要项目,而这些表面的设计基准一般都是轴的中心线,如果用两顶尖孔定位,就能符合基准重合的原则,而且能够最大限度地在一次安装中加工出多个外圆和端面,符合基准统一原则。当不能用两顶尖孔定位时,可采用轴的外圆表面作为定位基准,或以外圆表面和顶尖孔共同作为定位基准[3]。
根据本厂的实际情况,为了在简化加工工艺的基础上提高细长轴的加工精度,实际加工中采用了一夹一顶的装夹方式。即一端采用卡盘而另一端采用顶尖装夹,尾座顶尖采用弹性顶尖,可以使工件在轴向自由伸长。
3.2 切削加工过程
细长轴类零件的粗加工和半精加工通常采用车削。在车削加工过程中,工艺系统在切削力、夹紧力、重力、传动力、惯性力的作用下会产生不同程度的变形,使刀具与工件之间的相对位置发生变化,从而造成加工误差,机床、夹具、刀具的受力变形较小可以忽略不计,则工艺系统的变形将完全取决于工件的变形,因此增加细长轴类零件的的刚性尤为重要[3]。为了改善细长轴类零件的切削加工效果,采取了以下工艺优化:
3.2.1 掌握三个关键技术
车削加工中的三个关键技术即中心架和跟刀架的使用、解决工件热变形伸长以及合理选择车刀几何形状。
3.2.1.1 使用跟刀架支承细长轴
跟刀架是车削细长轴类零件极其重要的附件。采用跟刀架能提高工件的刚性,防止工件弯曲变形,抵消加工时径向切削分力的影响,从而减少切削振动和工件变形,但必须注意仔细调整,保证跟刀架的支撑爪和工件表面保持良好的接触,跟刀架的中心与机床顶尖中心保持一致[3]。从跟刀架的设计原理来看,只需两只支承爪就可以了,因车刀给工件的切削抗力使工件贴在跟刀架的两个支承爪上。但是实际使用时,工件本身有一个向下重力,以及工件不可避免的弯曲,因此,车削时工件往往因离心力瞬时离开支承爪、接触支承爪而产生振动。故需根据实际情况采用合适的跟刀架。使用时先把跟刀架用螺钉固定在大滑板上,跟在车刀后面,随车刀进给移动,以抵消背向力,增加工件的刚性,减小变形,从而提高细长轴的形状精度,并减小表面粗糙度[4]。
3.2.1.2 减少工件热变形伸长
车削时,由于切削热的影响,使工件随温度升高而逐渐伸长变形,这就叫“热变形”。在车削一般轴类时可不考虑热变形伸长问题,但是车削细长轴时,因为工件长,总伸长量长,所以一定要考虑到热变形的影响。故在实际加工细长轴时必须从以下三方面来解决细长轴热变形伸长问题。
(1)使用弹性回转顶尖。用弹性回转顶尖加工细长轴,可有较地补偿工件的热变形伸长,工件不易弯曲,车削可顺利进行。
(2)加注充分的切削液。车削细长轴时,不论是低速切削还是高速切削,为了减少工件的温升而引起热变形,必须加注切液充分冷却。使用切削液还可以防止跟刀架支承爪拉毛工件,提高刀具的使用寿命和工件的加工质量。
(3)刀具保持锐利。这样可以减轻车刀与工件的摩擦,从而减少发热。
3.2.1.3 合理选择车刀几何形状
车削细长轴时,由于工件刚性差,车刀的几何形状对工件的振动有明显的影响。
(1)由于细长轴刚性差,为减少细长轴弯曲,要求径向切削力越小越好,而刀具的主偏角是影响径向切削力的主要因素,在不影响刀具强度情况下,应尽量增大车刀主偏角。车刀的主偏角一般取kr=80°~93°。
(2)为减少切削力和切削热,应该选择较大的前角,取ro=15°~30°。
(3)车刀前面应该磨有R11.5~3的断屑槽,使切削顺利卷曲折断。
(4)选择正刃倾角,取入=3°使切削屑流向待加工表面,并使卷屑效果良好。
(5)切削刃表面粗糙度要求在Ra0.4以下,并要经常保持锋利。
(6)为了减少径向切削力,应选择较小的刀尖圆弧半径(re<0.3mm)。倒棱的宽度也应选得较小,取倒棱宽br1=0.5f。
综合考虑以上三要素,对于纺织机械传动主轴,在实际加工过程中采用两爪跟刀架,弹性顶尖及YT15硬质合金车刀,其主偏角90°、前角15°、刃倾角+3°、切削刃的表面粗糙度在Ra0.4以上,保持锋利。
3.2.2 控制好车床三要素
车床三要素即切削深度,进给量及切削速度三要素。
3.2.2.1 切削深度αp
由于传动主轴为光圆,没有台阶面,车削时分三刀进行。第一刀先粗车外圆尺寸到φ43mm,第二刀半精车外圆尺寸到φ41.5mm,第三道精车外圆尺寸到φ40.5mm。即每次的切削深度变化为2mm-1.5mm-1mm。
3.2.2.2进给量f
进给量主要应根据工件表面质量要求而定,一般情况可选0.15 mm/r~0.16 mm/r。粗加工时选大些,精加工时可选小些[2]。
3.2.2.3切削速度V
提高切削速度有利于降低切削力,减少切削变形,但振动会随切削速度的增加而增大,所以,可选切削速度V=60 m/min~90 m/min,工件的长径比及材料韧性大时Vc选小值,进给量大时V要降低,反之,要提高[2]。
传动轴车加工工艺如下:
粗车:转速n =450~500r/min;切削深度αp =1.5~2mm;进给量f=0.3~0.4mm/r。
半精车:转速n = 450~500r/min;切削深度αp =1~1.5mm;进给量f=0.15~0.2mm/r。
精车:转速n = 500~550r/min;切削深度αp =0.5~1mm;进给量f=0.1~0.15mm/r。
4 细长轴磨加工工艺探讨
细长轴类零件的精加工通常采用磨削,磨削时采用两顶尖装夹。根据材料本身的特点(易弯曲、韧性高),选择合适的砂轮,进给量及冷却液。砂轮采用60#棕刚玉,粗精磨每次磨削深度均在0.02-0.03mm左右。先粗精磨一端且尽量接近总长,留一个砂轮宽度,精磨后调头粗精磨另一头。
5 结论
在影响细长轴加工精度的各种因素中,车加工是最主要的因素,而细长轴车加工精度的各种因素中,切削力是主要因素,为减小切削力所引起的变形,就要选好跟刀架,以增强其刚性,减小变形,还要选择合理的几何角度以减小改变走刀方向。
车削和磨削细长轴的难度较大,但它也有一定的规律性。在车削加工时,主要抓住中心架和跟刀架的使用、解决工件热变形伸长以及合理选择车刀几何形状等三个关键技术,控制好切削深度、走刀量、切削速度这三要素,问题就迎刃而解了。根据优化的车削及磨削工艺,成品主轴达到了要求的技术条件,即传动主轴的外径尺寸为φ40H8,表面粗造度Ra达到1.6以上,全长径跳均保持在0.02mm以下。
上一篇:加工细长轴车削时的注意事项
下一篇:他有一手车工“绝活”
联系我们
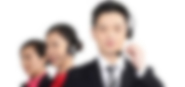
常州利刚机械有限公司
手机:13584568772
电话:13584568772
传真:0519-83205637
邮箱:1799591967@qq.com
地址:常州市新北区王下村工业园区